
Introduction to CNC Machining: A Cornerstone in Modern Manufacturing
Computer Numerical Control (CNC) Machining has become the cornerstone technology of precision manufacturing, revolutionizing how industries approach the fabrication of parts and components.
At its core, CNC Machining is an advanced manufacturing process where pre-programmed computer software dictates the movement of factory tools and machinery. Allowing for the automated, precise, and repeatable production of complex parts with a level of accuracy unattainable by manual machining.
Utilized across a myriad of sectors—including aerospace, automotive, and medical, and more—CNC Machining combines the prowess of computerized controls with the versatility of multi-axis tools, enabling the creation of intricate geometries that meet exacting specifications.
As experts in the field, Corbett Engineering leverages this sophisticated technology to deliver unparalleled precision, efficiency, and quality, ensuring our clients' manufacturing needs are not just met, but exceeded.
Defining CNC Machining in an Industrial Context
CNC Machining, a process at the forefront of industrial manufacturing, leverages computer numerical control to operate machine tools with unparalleled precision.
This method, pivotal for businesses in sectors like aerospace, automotive, and medical equipment, involves translating CAD (Computer-Aided Design) models into numerical instructions.
These instructions guide CNC machines to fabricate parts with exacting accuracy, crucial for industries where even minute deviations can have significant implications.
CNC Machining: A Strategic Asset for Diverse Industries
In the B2B realm, CNC Machining is not just a manufacturing process; it's a strategic asset.
It plays a critical role in industries requiring high-precision components, such as aerospace, where tolerances are tight and material integrity is paramount. In the automotive sector, it accelerates production while adhering to rigorous quality standards.
For businesses specializing in custom manufacturing, CNC Machining offers the flexibility to produce small batches without compromising on quality or efficiency.
The Technical Edge of CNC Machining
CNC Machining's core advantage lies in its precision and repeatability, essential for high-volume production runs where consistency is key.
The technology enables the production of complex geometries that manual machining methods cannot achieve, offering a competitive edge in manufacturing intricate components.
Furthermore, CNC Machining enhances operational efficiency by reducing manual labor and minimizing errors, leading to cost-effective production cycles.
Navigating the Future of Manufacturing with CNC Machining
Our goal is to offer our insights and knowledge to empower businesses to make informed decisions in their manufacturing processes, leveraging CNC Machining for optimal outcomes.
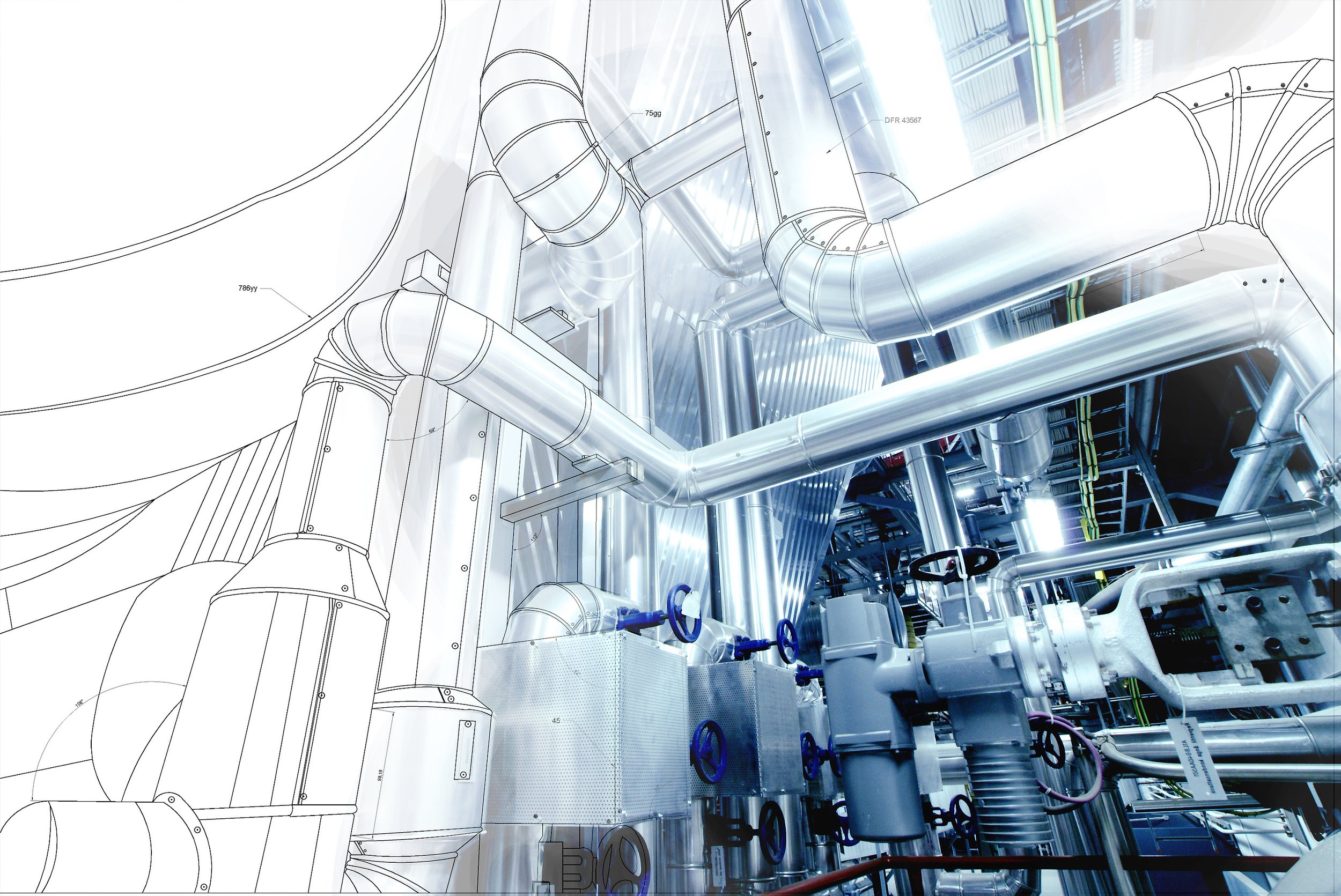
The Technical Workings of CNC Machining
This “process” of CNC Machining begins with a Computer-Aided Design (CAD) model - a detailed 3D digital representation of a physical object, created using CAD software to facilitate precision engineering, analysis, and manufacturing.
This model is then converted into a set of numerical instructions known as G-code, instructions that guide advanced CNC tools like grinders, lathes, and mills, to cut and shape material with extreme accuracy, and capable of moving along multiple axes.
The result is an ability to produce highly complex, precise, and consistent parts that meet the exact specifications and tight tolerances of a diverse range of industries with minimal waste and optimal efficiency.
By automating the machining process, CNC technology not only enhances efficiency and reduces the potential for error but also opens up new possibilities in design and innovation, making it a pivotal tool in today's manufacturing landscape.
Precision Programming: The Heart of CNC Machining
CNC Machining begins with precise programming, where engineers convert CAD designs into CNC language (G-code). This programming is the blueprint for the machining process, dictating every movement of the machine with exact coordinates.
The precision of CNC programming allows for tight control over factors like speed, position, and feed rate, ensuring each part meets exact specifications.
CNC Machines: Types and Capabilities
In the world of CNC Machining, diverse machine types cater to various manufacturing needs:
CNC Mills
These machines handle a wide range of operations, from simple cuts to complex parts with multiple axes.
CNC Lathes or Turning Centers
Best for cylindrical parts, these machines offer high precision in turning operations.
CNC Routers
Ideal for cutting softer materials like wood, plastic, and some metals, routers are used extensively in custom fabrication.
CNC Grinders
Used for finishing operations, ensuring surface quality and dimensional accuracy.
Each type of CNC machine brings unique capabilities to the manufacturing floor, allowing businesses to select the most suitable machine for their specific production requirements.
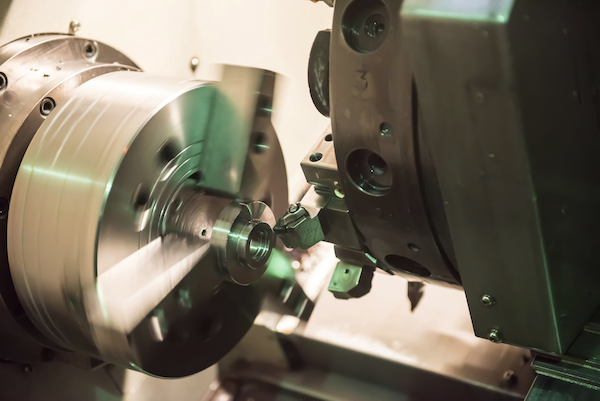
The Machining Process: From Raw Material to Finished Product
The CNC Machining process involves several key steps:
Setup and Calibration: Machines are set up with the appropriate tools and calibrated for the specific operation.
Material Loading: Raw materials are loaded into the machine. This can be metals, plastics, or composites, depending on the product requirements.
Machining Operations: The machine executes the programmed instructions, cutting and shaping the material into the final part.
Quality Assurance: Post-machining, parts undergo rigorous inspection to ensure they meet the predefined specifications.
Advantages in Efficiency and Consistency
CNC Machining stands out for its efficiency and consistency, especially in high-volume production. The automation of the machining process reduces human error and increases throughput.
Additionally, the ability to run machines for extended periods without intervention makes CNC Machining ideal for meeting tight production deadlines.
Advantages of CNC Machining in Modern Manufacturing
High Precision and Consistency
One of the most significant advantages of CNC Machining is its ability to produce parts with extremely high precision. This is crucial in industries where parts must adhere to strict specifications, such as in aerospace or medical device manufacturing. CNC machines operate with a level of accuracy that manual machining processes cannot match, ensuring consistency across high-volume production runs.
Enhanced Efficiency and Productivity
CNC Machining dramatically enhances manufacturing efficiency. Once a part is designed and the machine is programmed, it can produce that part repeatedly with minimal variance. This automation reduces the time and labor involved in producing each part, leading to increased productivity and the ability to meet tight production schedules.
Flexibility in Design and Prototyping
The versatility of CNC Machining allows for the production of complex designs that would be difficult or impossible to achieve with traditional machining. This flexibility is particularly beneficial in prototyping, where modifications to design can be made quickly and without significant additional cost. For businesses, this means faster time-to-market for new products and the ability to easily customize parts.
Reduced Waste and Cost-Effectiveness
CNC Machining is also more resource-efficient, generating less waste material compared to conventional machining. The precision of CNC machines means that raw materials are used more efficiently, contributing to cost savings, especially in large-scale production. Additionally, the reduced need for manual labor and the decrease in errors further contribute to cost-effectiveness.
Improved Safety and Reduced Labor Intensity
With CNC Machining, the direct human interaction with the cutting tools is minimized, enhancing safety on the manufacturing floor. This automation reduces the physical strain on workers and lowers the risk of accidents, creating a safer work environment.
The advantages of CNC Machining make it a cornerstone technology in modern manufacturing. Its precision, efficiency, and flexibility provide businesses with the tools to produce high-quality parts, optimize production processes, and stay competitive in a rapidly evolving industrial landscape.
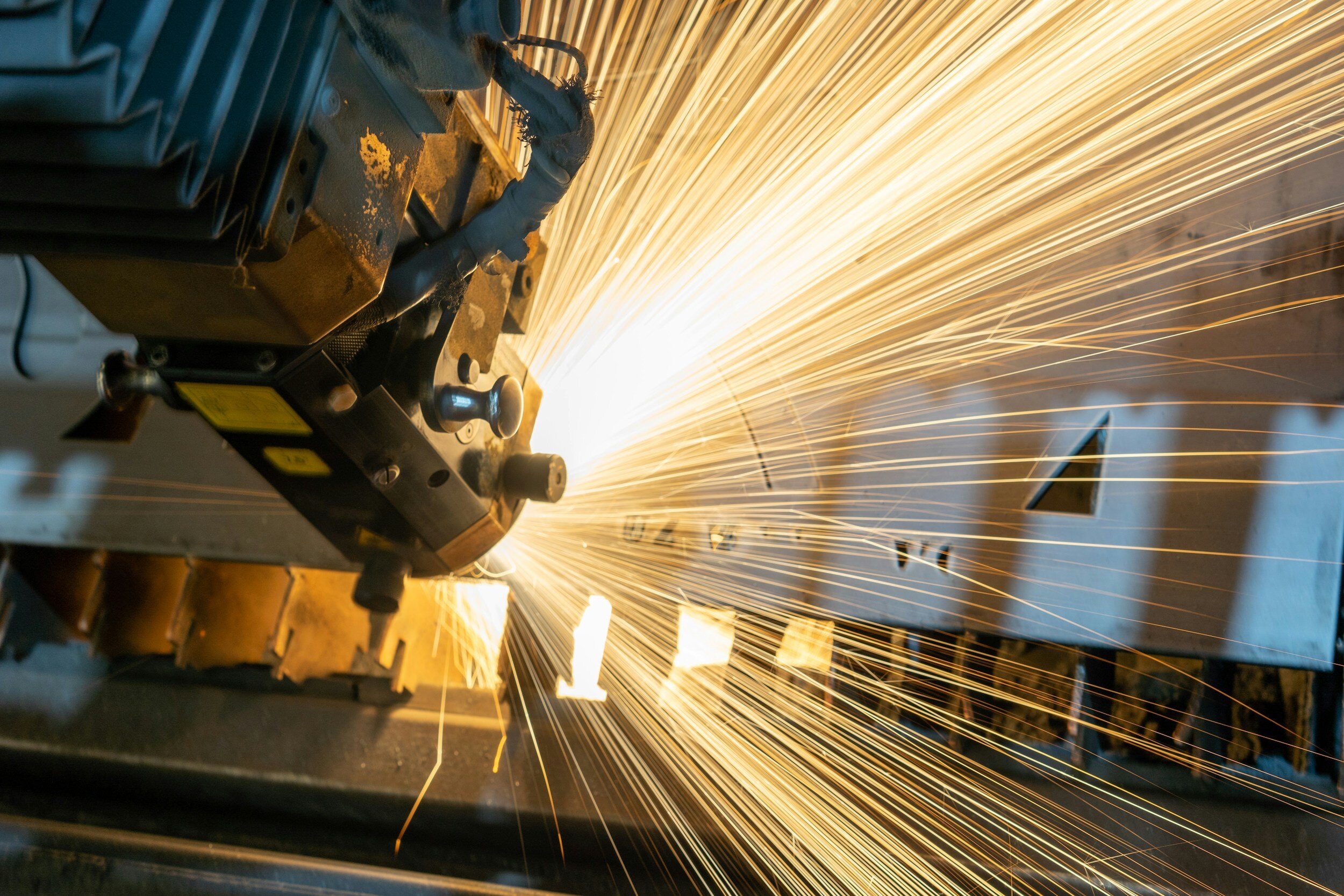
Exploring Types of CNC Machines and Their Applications
CNC Mills: Versatility for Complex Geometries
CNC mills are arguably the most versatile type of CNC machines. Equipped with various cutting tools, they are capable of performing a wide range of operations such as drilling, milling, and tapping. They are particularly adept at creating complex geometries and are essential in industries requiring intricate designs, like aerospace and automotive.
Vertical Mills: Feature a vertically oriented spindle, ideal for plunge cuts and drilling.
Horizontal Mills: Best for heavy cutting operations, offering advantages in chip evacuation and ability to machine three sides of the part in one set up.
CNC Lathes or Turning Centers: Precision in Cylindrical Parts
CNC lathes, also known as turning centers, are specialized for producing precise cylindrical parts. They rotate the workpiece against a stationary cutting tool, making them ideal for applications where round or tubular shapes are required, such as shafts or rods in automotive or industrial machinery.
Multi-Axis Lathes: Offer additional axes for more complex operations, reducing the need for secondary machining.
CNC Routers: Ideal for Soft Materials
CNC routers are commonly used for cutting softer materials like wood, plastics, composites and some non-ferrous metals. They are prevalent in woodworking, sign making, and in the production of non-metallic components for various industries.
3-Axis Routers: Suitable for general cutting and carving tasks.
5-Axis Routers: Provide the ability to work on complex shapes and undercuts.
CNC Grinders: Achieving Surface Finish and Precision
CNC grinders use a rotating grinding wheel to remove material, achieving a high-quality surface finish and precise control of the shape and dimension. They are crucial in applications requiring high surface quality and precision, like finishing automotive parts or creating specialized tools.
EDM Machines: Specialized in Hard Materials
Electrical Discharge Machining (EDM) is a specialized type of CNC machining used to cut hard materials that are difficult to machine with traditional methods. EDM is invaluable in mold-making, tool-making, and machining complex shapes in hardened materials.
Understanding the different types of CNC machines and their specific applications is crucial in selecting the right equipment for your manufacturing needs.
Each type offers unique capabilities, making them suitable for various applications across a wide range of industries. By choosing the appropriate CNC machine, businesses can optimize their manufacturing processes, enhance product quality, and improve overall efficiency.
What to Consider When Choosing a CNC Machine Shop.
Understanding Your Manufacturing Needs
The first step in selecting a CNC machine is to thoroughly understand your manufacturing needs. Consider the types of parts you will be producing, the materials you will be working with, and the volume of production. Different CNC machines are optimized for different tasks, materials, and production scales.
Types of Parts and Complexity
For complex parts with intricate geometries, a 5-axis CNC machine may be necessary.
If your focus is on simpler parts, a 3-axis machine might suffice.
Material Compatibility
Heavy-duty machines are required for hard materials like metals, while softer materials like plastics and wood can be machined on less robust machines.
Consider the material's properties, such as hardness and abrasiveness, as they impact the type of machine and tooling required.
Volume of Production
High-volume production demands machines with higher automation and efficiency.
For lower volumes or custom jobs, a more versatile and easily reconfigurable machine might be more appropriate.
Precision Requirements
The required precision level is a critical factor. Industries like aerospace and medical devices demand extremely high precision, necessitating advanced machines with higher accuracy.
Budget and ROI Considerations
Assess the cost of the machine against the expected return on investment (ROI).
Consider not only the initial purchase price but also the ongoing operational and maintenance costs.
Ease of Use and Software Compatibility
User-friendly interfaces and compatibility with your existing CAD/CAM software are important for seamless integration into your workflow.
Training requirements for operating the machine should also be considered.
Future-Proofing Your Investment
Look for machines that offer scalability and flexibility to adapt to future needs.
Consider the machine's ability to integrate with emerging technologies and automation.
Choosing the right CNC machine is a strategic decision that can significantly impact your business's operational efficiency and product quality.
By carefully considering your manufacturing needs, material requirements, precision levels, budget constraints, and future scalability, you’ll make sure to select a CNC machine that not only meets your current needs but also supports your business's growth and evolution.
Elevate Your Manufacturing with Corbett Engineering's CNC Expertise
As we've explored the intricate world of CNC Machining, it's clear that this technology is not just about precision and efficiency; it's about pushing the boundaries of what's possible in modern manufacturing.
At Corbett Engineering, we understand the critical role CNC Machining plays in driving innovation and competitiveness in today's industrial landscape.
Our commitment to excellence in CNC Machining is not just about providing state-of-the-art technology; it's about partnering with you to transform your manufacturing processes. With Corbett Engineering, you gain more than a service provider; you gain a partner who is invested in your success.
Our expertise in CNC Machining encompasses a deep understanding of the technology, a commitment to quality, and a focus on tailored solutions that meet your unique business needs.
We invite you to reach out and discover how partnering with Corbett Engineering can bring unparalleled value to your operations. Whether you're looking to enhance precision, increase efficiency, or innovate your product offerings, our team is ready to help you achieve your manufacturing goals.
Contact us today to learn more about how Corbett Engineering's CNC Machining capabilities can be the catalyst for your business's next big leap forward.